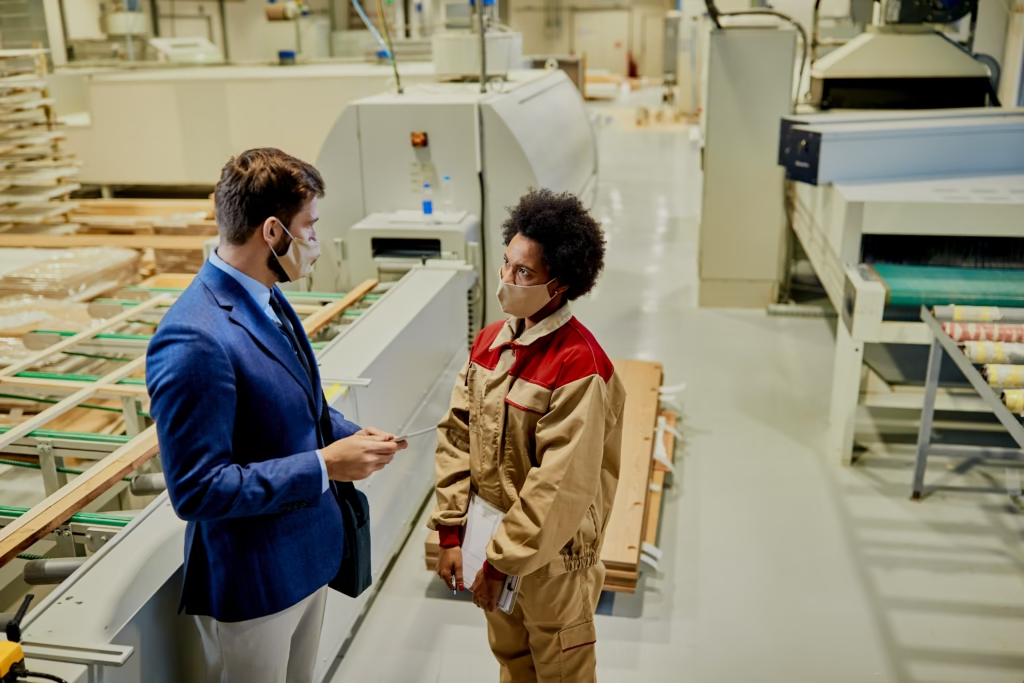
Time studies are a vital tool in the industrial engineer’s arsenal, enabling us to uncover inefficiencies, set benchmarks, and drive continuous improvement. But, as straightforward as they might seem, time studies are riddled with potential pitfalls that can lead to inaccurate data, misguided conclusions, and wasted resources. Over the years, I’ve seen these mistakes firsthand—sometimes learning the hard way. Here are 10 common time study mistakes and how to avoid them to ensure your efforts translate into real process improvements.
1. Incomplete Preparation
One of the most common mistakes is diving into a time study without thorough preparation. Skipping this step can lead to missed data or improper focus. I once conducted a time study without first reviewing the process—only to realize halfway through that I hadn’t accounted for a critical setup phase.
Avoidance Tip: Familiarize yourself with the process beforehand. Use process maps or walkthroughs to understand the steps, tools, and variables involved before starting the study.
2. Not Accounting for Variability
Processes rarely run the same way every time. Failing to capture variability—due to worker behavior, machine performance, or external factors—can result in flawed conclusions.
Avoidance Tip: Conduct multiple observations over varying conditions to capture a representative sample of the process.
3. Ignoring Non-Value-Added Activities
A common trap is focusing only on the “value-added” parts of a process while overlooking delays, waiting times, and other non-value-added activities. These often hold the key to unlocking efficiency.
Avoidance Tip: Pay attention to all activities, including idle times, material handling, and rework.
4. Observer Bias
Workers often alter their behavior when they know they’re being observed, leading to “Hawthorne effect” distortions. I’ve seen production rates improve dramatically during a time study, only to return to normal afterward.
Avoidance Tip: Use discrete observation methods, such as video recordings, and aim to blend into the background to reduce observer influence.
5. Using the Wrong Tools
Outdated or inappropriate tools—such as relying solely on a stopwatch when video analysis is needed—can limit the accuracy and utility of your study.
Avoidance Tip: Choose tools that fit the complexity of the process. Modern technologies like video analysis software and wearable sensors can significantly enhance data collection.
6. Poor Element Definition
Vague or poorly defined process elements can make it impossible to collect consistent data. For example, I once measured “assembly time” without breaking it down into its subcomponents, making it difficult to pinpoint inefficiencies.
Avoidance Tip: Define each process element clearly and ensure everyone involved understands these definitions.
7. Failing to Involve Operators
Operators often have critical insights into the process, but many time studies overlook their input, leading to missed context and resistance to change.
Avoidance Tip: Involve operators from the start. Their knowledge can help you refine your observations and identify realistic improvement opportunities.
8. Overlooking External Influences
Factors like material availability, environmental conditions, or upstream delays can skew results if they aren’t accounted for.
Avoidance Tip: Document external factors during the study and consider their impact on the observed times.
9. Setting Unrealistic Expectations
Time studies can sometimes lead to overly ambitious targets or expectations, causing frustration and disengagement among workers.
Avoidance Tip: Use the data to set achievable goals. Consider factors like fatigue, learning curves, and natural variations in performance.
10. Neglecting Follow-Up and Validation
Collecting time study data is only the first step. Failing to validate the results or implement changes renders the effort meaningless. Early in my career, I conducted a study and shared my findings, assuming they’d be acted upon—but no follow-up occurred, and the inefficiencies remained.
Avoidance Tip: Validate your findings with stakeholders and create an action plan for implementing improvements. Follow up regularly to measure progress.
Final Thoughts
Time studies are a powerful tool, but only if conducted thoughtfully and systematically. By avoiding these 10 common mistakes, you can ensure your time studies lead to actionable insights and measurable improvements. Remember, every study is an opportunity to learn not just about the process but also about how to refine your approach as an industrial engineer. Stay curious, involve your team, and always strive for continuous improvement.
Leave a Reply