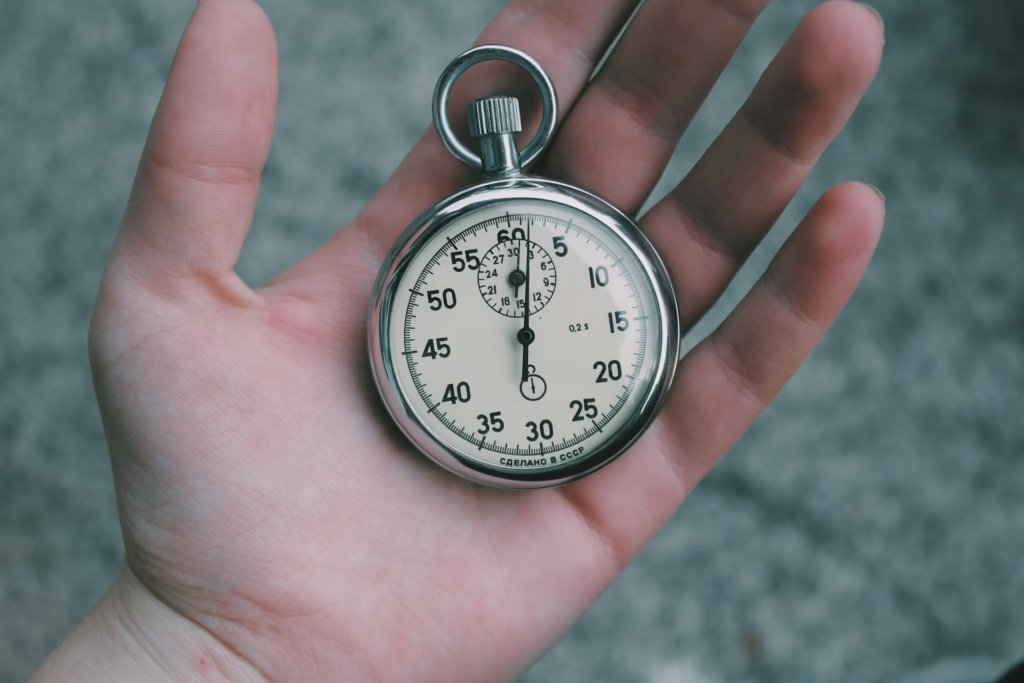
In the fast-paced world of industrial engineering, optimizing processes is key to staying competitive. Advanced time studies and process mapping are powerful tools that enable engineers to enhance operational efficiency and productivity. In this article, we will explore advanced techniques in time studies, how to effectively map processes, and provide practical examples to help you implement these strategies in your work.
Understanding Advanced Time Studies
Advanced time study techniques go beyond traditional stopwatch methods by incorporating technology and data analytics. Here are some techniques:
- Video Analysis: Utilizing video recording to analyze tasks and identify inefficiencies. This method allows for detailed examination of body movements and task flow.
- Motion Study Software: Software tools like MOST (Maynard Operation Sequence Technique) and MTM (Methods-Time Measurement) help in analyzing and standardizing work processes to improve productivity.
Process Mapping: Visualizing Efficiency
Process mapping is essential for visualizing workflows and identifying bottlenecks. Techniques include:
- Flowcharts: Simple visual representations of processes to highlight each step and decision point.
- Value Stream Mapping: A lean-management method used to analyze and design the flow of materials and information required to bring a product to a consumer.
Practical Examples and Software Tools
- Video Analysis Example: A leading electronics manufacturer used video analysis to streamline assembly line tasks, reducing cycle time by 15%.
- Motion Study Software Example: A global automotive company applied MOST to standardize workstation setups, leading to a 20% increase in productivity.
Conclusion
Advanced time studies and process mapping are indispensable in modern industrial engineering. By leveraging these techniques and technologies, engineers can drive efficiency and achieve significant operational improvements. Stay ahead by continuously refining your processes and embracing innovation.
Leave a Reply