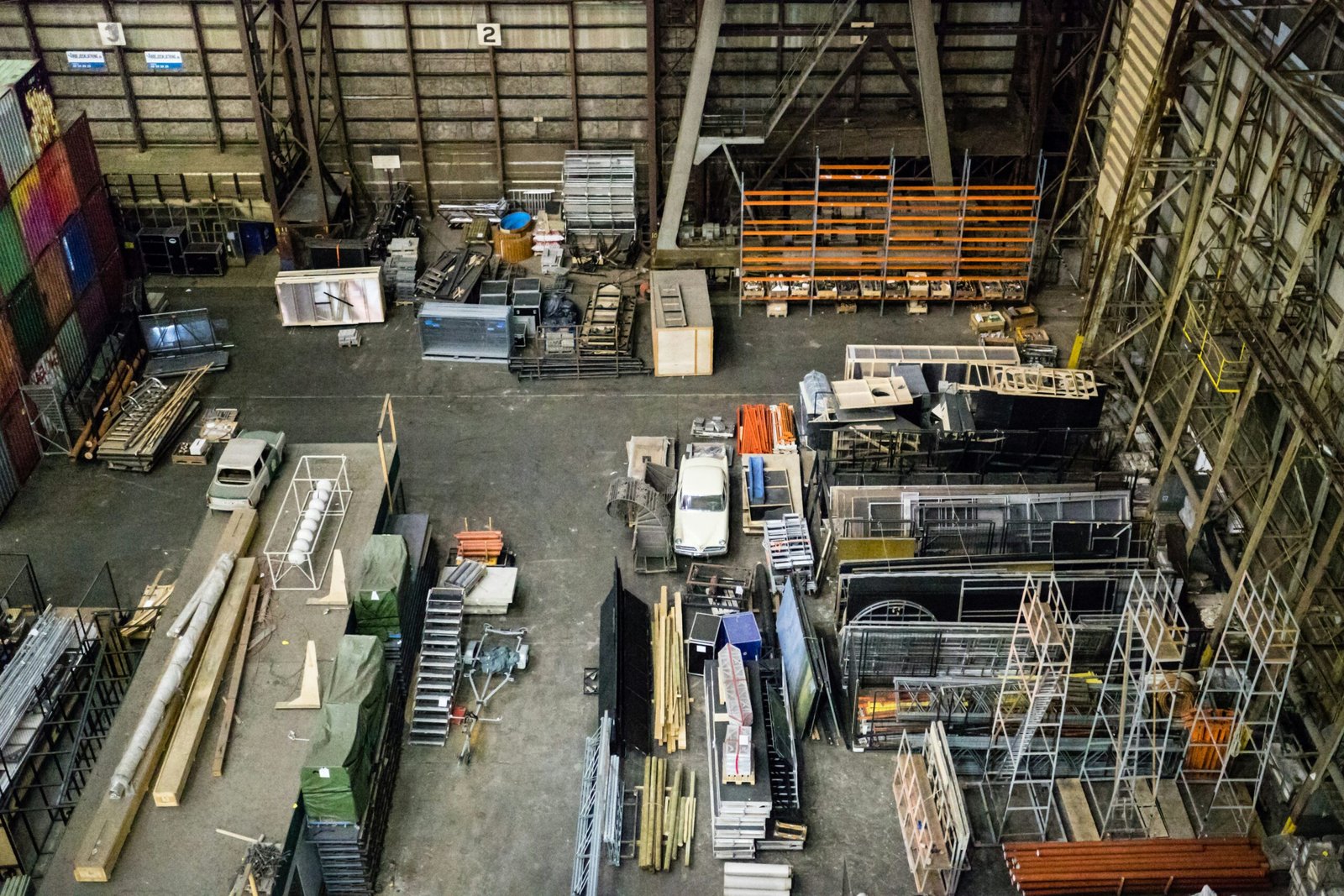
What is 5S?
5S is a structured workplace organization method that boosts efficiency and productivity. It originated in Japan and is a key part of Lean manufacturing. The term “5S” represents five steps: Seiri (Sort), Seiton (Set in Order), Sōji (Shine), Shitsuke (Standardize), and Seiketsu (Sustain). These steps help create and maintain an organized workspace.
The goal of 5S is to reduce waste, improve workflow, and enhance safety. By following these steps, businesses can streamline operations and foster a culture of continuous improvement. Many industries, including manufacturing and logistics, use 5S to boost efficiency and organization.
The 5S Principles
- Sort: Identify and remove unnecessary items. Clutter distracts workers and reduces efficiency. Keeping only essential tools and materials creates a more productive environment.
- Set in Order: Organize necessary items for easy access. Logical placement of tools and supplies saves time and prevents disruptions. Labeled storage areas and visual cues can further enhance efficiency.
- Shine: Clean and maintain the workspace. A clean environment reduces safety risks and helps spot equipment issues early. Regular maintenance improves longevity and reliability.
- Standardize: Establish clear procedures for consistency. Well-documented workflows ensure tasks are performed correctly and efficiently. Standardization also simplifies training and onboarding.
- Sustain: Maintain and reinforce 5S practices. Ongoing training, regular audits, and leadership support help embed these habits into workplace culture. Without sustainment, improvements can fade over time.
5S isn’t just about organization—it’s about creating a disciplined, efficient, and safe workplace. When applied consistently, it leads to significant productivity gains.
5S in a Manufacturing Environment
At XYZ Manufacturing, inefficiencies slowed production. Management launched a 5S initiative to fix the problem.
- Sort: Employees removed outdated tools and paperwork. Eliminating excess clutter simplified workflows.
- Set in Order: Frequently used tools were assigned designated spots. This system reduced downtime caused by searching for materials.
- Shine: Regular cleaning schedules improved safety and workplace conditions. Employees also identified and addressed maintenance issues faster.
- Standardize: Labels, color coding, and standardized work procedures reduced confusion. Consistent processes minimized operational inconsistencies.
- Sustain: Ongoing training and audits reinforced the changes. Managers encouraged a culture of continuous improvement.
The results? A 20% productivity increase and higher employee morale. Workers felt more engaged and took greater pride in their workspace.
5S in a Shipping Dock Environment
A logistics company faced frequent shipment errors and slow processing due to disorganization. Adopting 5S transformed their shipping dock.
- Sort: Employees removed non-essential items, clearing pathways and improving workflow. Less clutter meant faster, more accurate shipments.
- Set in Order: Tools and materials were assigned specific locations. Clearly marked zones reduced time wasted searching for supplies.
- Shine: Routine cleaning schedules kept the dock safe and well-maintained. Employees took ownership of keeping their work areas tidy.
- Standardize: The company implemented clear operating procedures for handling shipments. Consistent methods reduced errors and improved efficiency.
- Sustain: Ongoing training and audits reinforced 5S principles. Regular check-ins ensured lasting adherence to the system.
The impact? Faster processing times, 30% fewer shipment errors, and improved employee morale. 5S proved its effectiveness beyond manufacturing, enhancing operations in logistics and other industries.
Leave a Reply